Ultrafilter® International
Three Main Steps for Compressed Air Purification
Compressed Air Uses and Quality Standards (ISO/DIS8573-2)
Application Guide Typical Application Setup
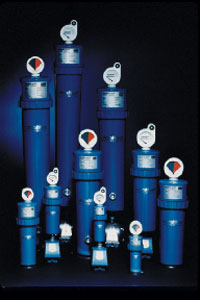
- Drying
- Filtration
- Condensate management
Based upon the class of air desired for your application, you will need various combinations of drying and filtration products to produce the compressed air effluent quality.
Condensate (runoff) formed by the system may contain oil and other by-products—dispose properly to avoid contamination of the environment.
Class | Oil (ppm) | Water (dew point) | Dirt (µ) | Typical applications |
1 | 0.01 | -100°F | 0.1 | Highly sensitive equipment, critical applications |
2 | 0.1 | -40°F | 1 | Instrument quality air— instrumentation, automation, process air, paint systems |
3 | 1 | -4°F | 5 | Pneumatic machinery, air tools |
4 | 5 | 35°F | 15 | General purpose—shop air |
5 | 25 | 45°F | 40 |
6 | — | 50°F | — |
Dirty, wet compressed air may contain four million particles per cubic foot and 0 to 100 ppm of oil; may hold rust, viruses, and odors; and may be 100% saturated with water. The chart below will help you select the best air filtration system for your application.
Type of air | Examples | Recommended filter stages (in sequence) |
Clean | General use, blow guns, simple robotics, air gauging, fine pneumatic tools | Prefilter (1) and microfilter (3) |
Clean and odor free | Blow moulding, simple breathing air, instrumentation, | Prefilter (1), microfilter (3), and activated carbon filter (4) cosmetics, food packaging, dairy production |
Clean with reduced dew point | Good factory air, air gauging, conveying, shot blasting, fluidics | Prefilter (1), dryer (2), and microfilter (3) |
Clean and dry | Air bearings, fluidic sensors, paint spraying, critical control air, | Prefilter (1) , dryer (2), microfilter (3), and sterile filter (5) cold atmospheric conditions |
Sterile air | Process contact air, pharmaceutical, food/beverage, dairy, hospitals | Prefilter (1), dryer (2), microfilter (3), activated carbon (4), sterile filter (5), and steam sterile filter (6) [for cleaning the sterile filter] |
Note 1: The prefilters (1) and microfilters (3) come with a condensate autodrain (8) attached to the bottom of the housing.
Note 2: The oil/water separators (7) can be attached to the outlet drains of the prefilter (1) and microfilter (3) if there are any oil particulates in the line. This will separate the oil condensate from the water condensate so the water can be disposed without harming the environment.
- Determine the quality of air you need for your application using the application guide below.
- Use the illustration to determine the components you will need to meet your desired effluent quality.
- Size the components on the following pages per the inlet flow and pressure of your application and your desired effluent quality.
Typical Application |
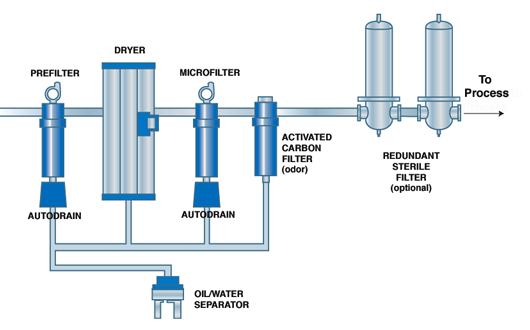 |
Note: Where noted (on product page), desiccant dryers come with a prefilter, microfilter, and autodrain. For those that don't, those components must be purchased separately as shown in the diagram. |
Disclaimer: Cole-Parmer products are not approved or intended for, and should not be used for medical, clinical, surgical or other patient-oriented applications.